Projects
Silica
High purity silica sand is a valuable industrial mineral used for frac sand, glass manufacturing, fiberglass, high temperature well cement, water filtration, and locomotive traction sand.
Immediate Goal: To build a mine for industrial silica, frac sand, and ground silica well cement retrogression inhibitor. A production level of 300,000 tons per year would generate ≈ $10 million/year revenue. Production development for advanced silica materials will be driven by cash flow from silica materials.
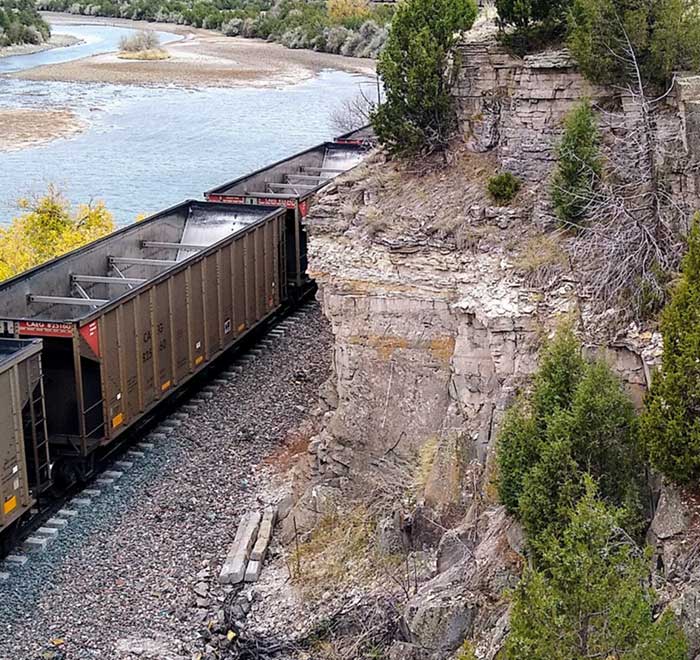
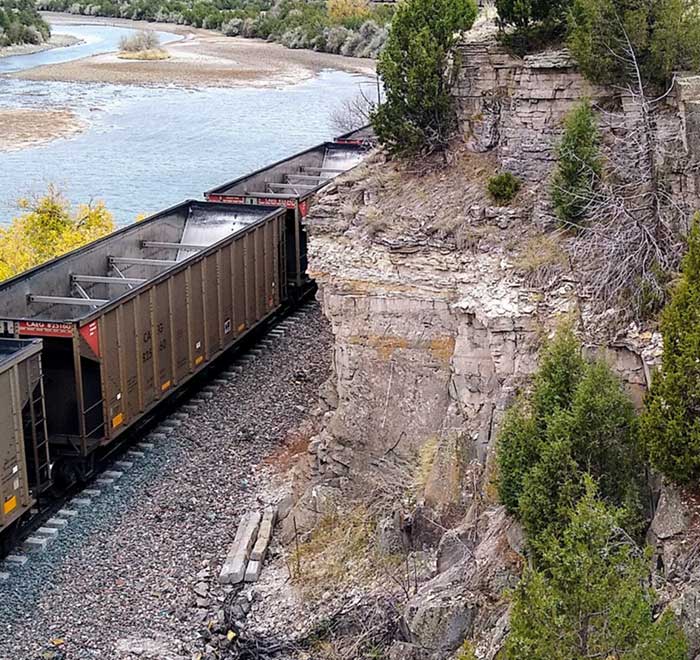
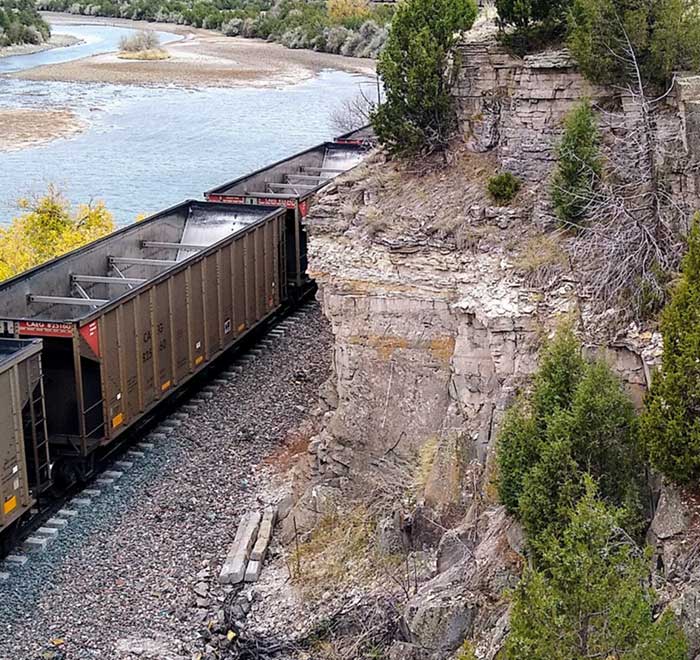
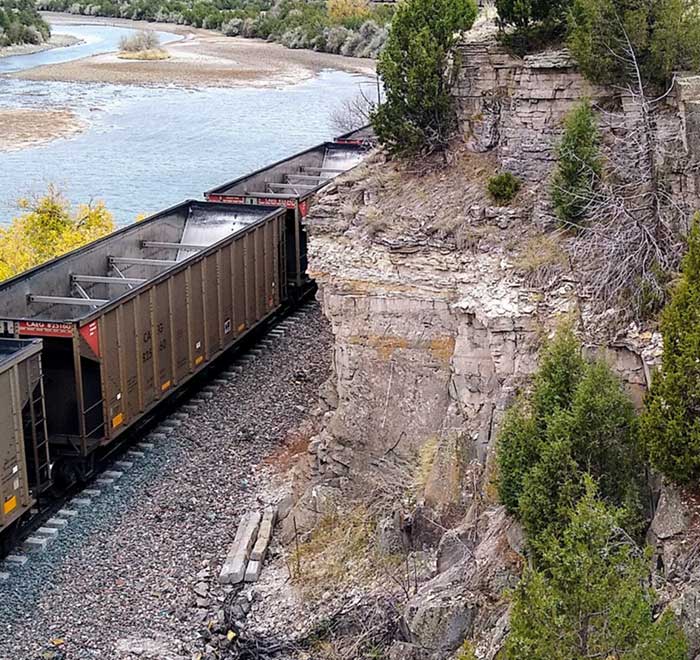
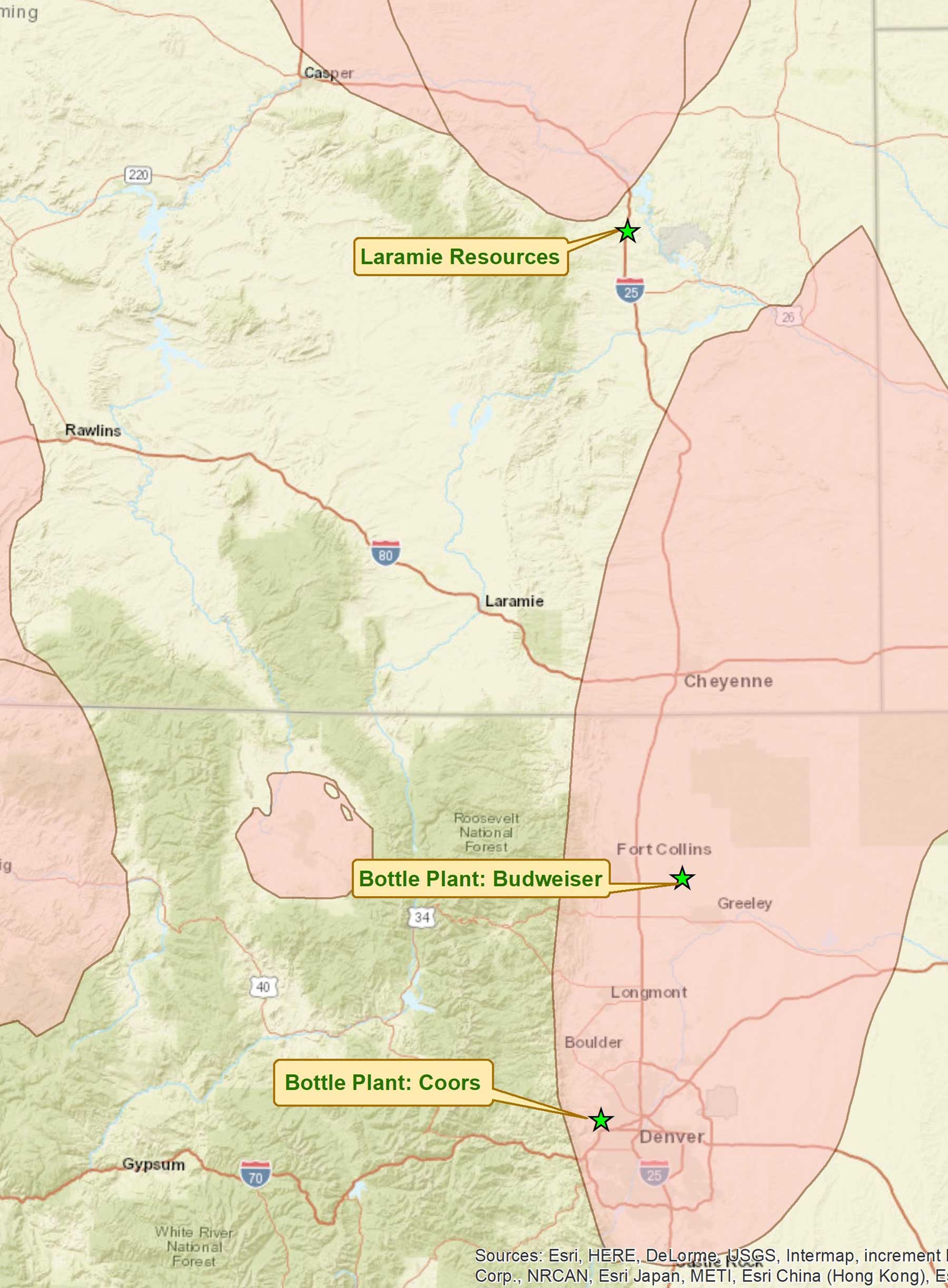
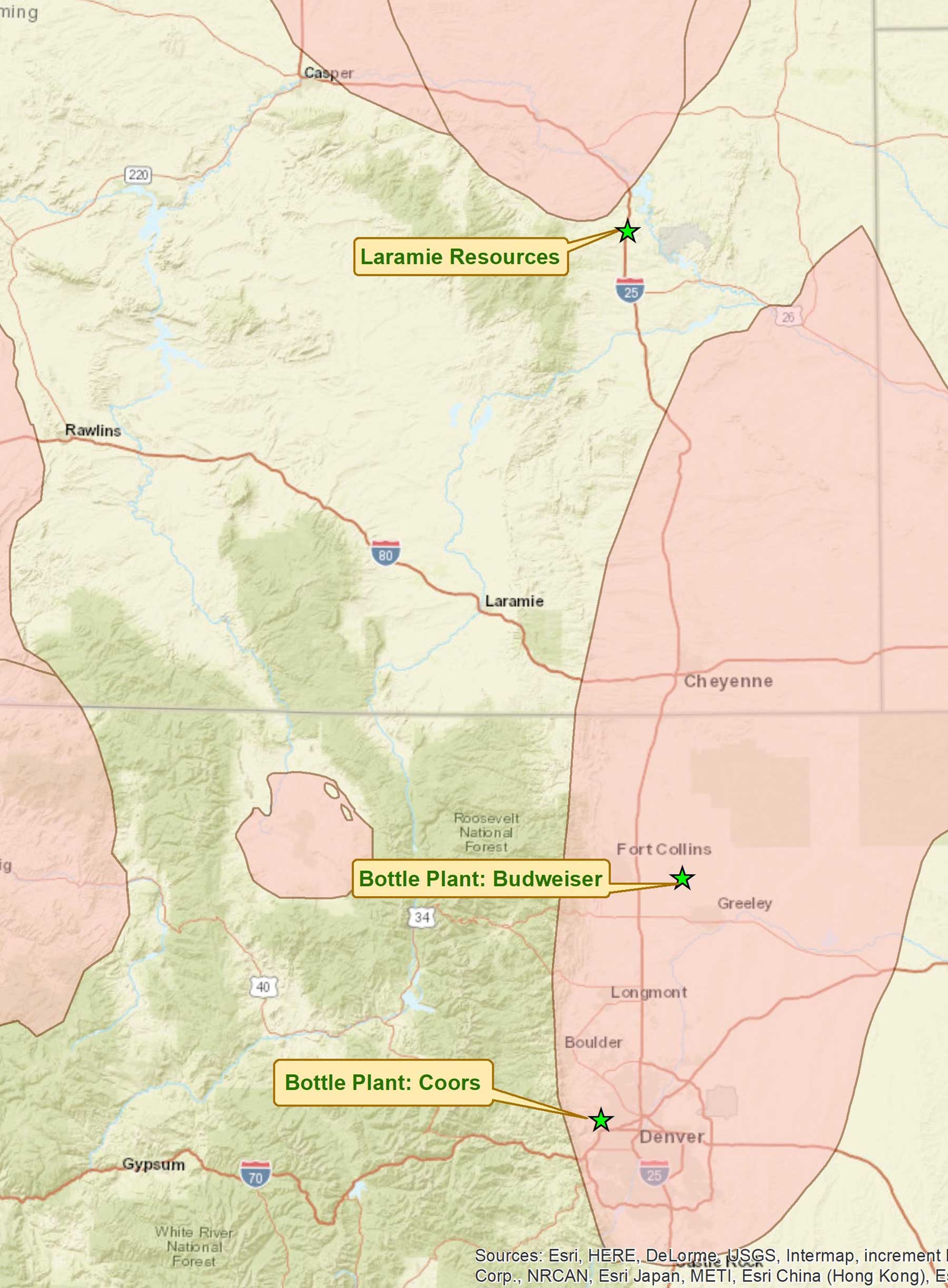
- Two separate deposits, each over 20 million tons, offer many years of supply.
- There are no producers of high-purity silica within 750 miles of our target customers.
- Rail transport cost of glass and other industrial silica products into the region is $28-50/ton, which comes with potential service disruption risk.
- A regional source can cut total delivered silica costs by as much as 50% while offering just-in-time delivery.
- Extensive data from past work informs our product confidence.
- Our high purity silica is proven for glass making, high crush strength, and is a unique raw material for high value products.
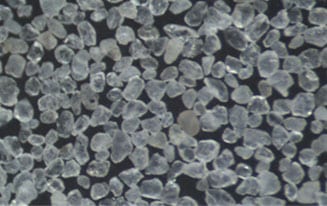
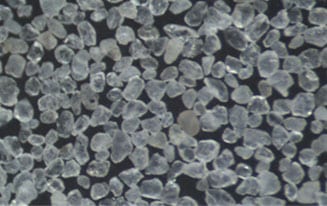
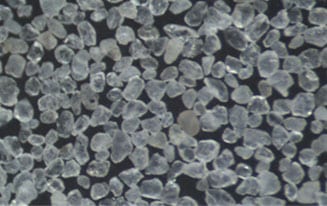
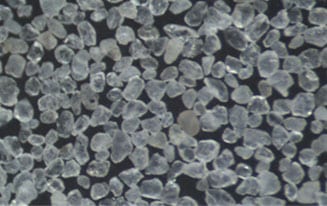
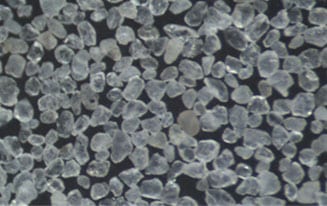
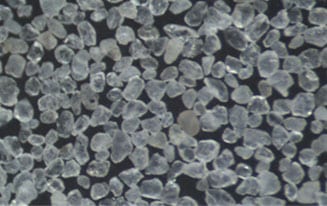
Sunrise Iron
Brownfield vs. opportunity: The difference is information and insight
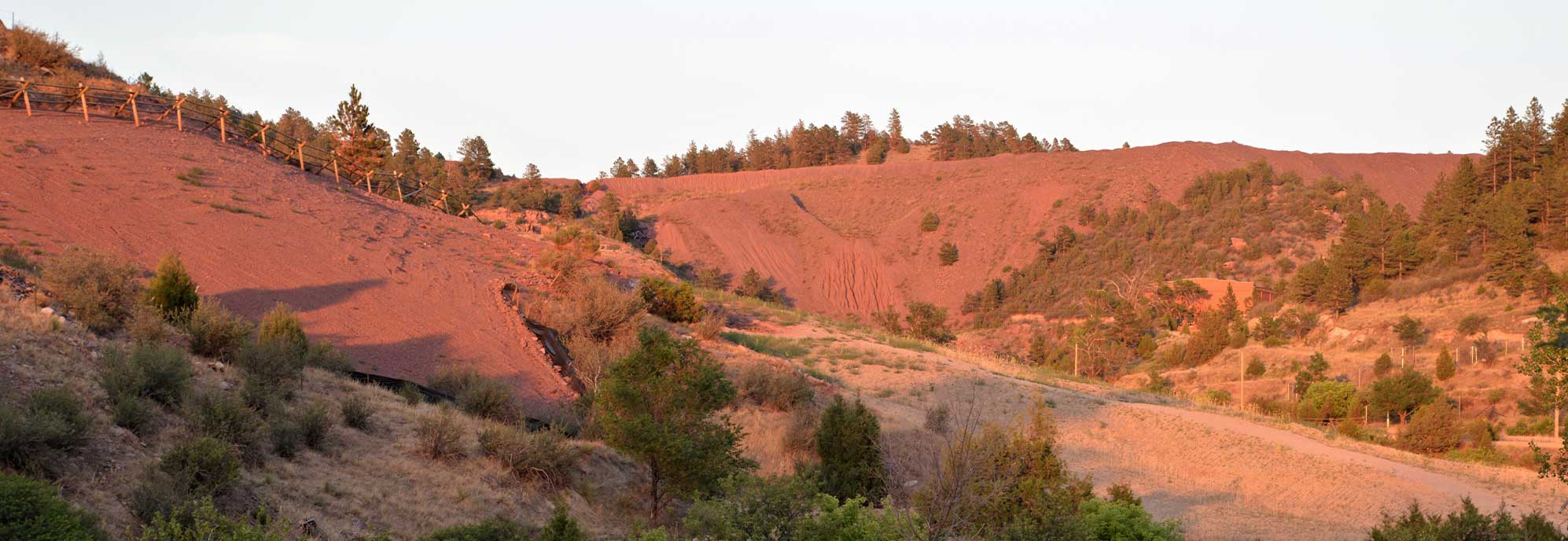
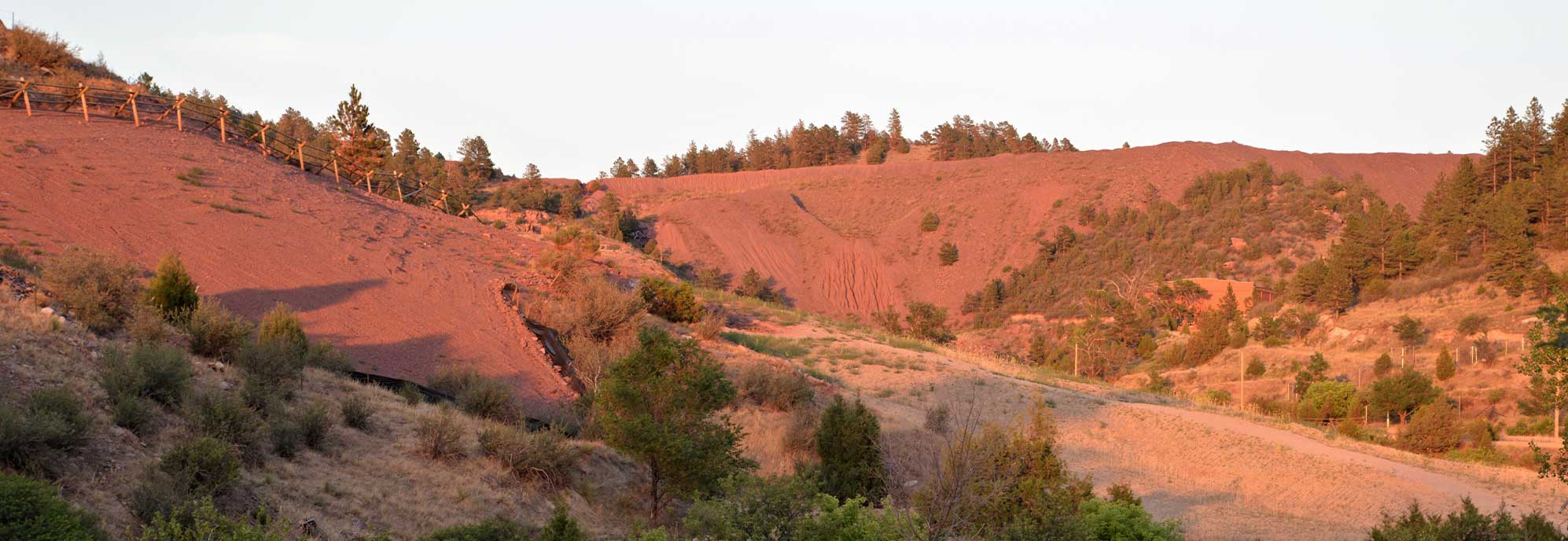
People have been collecting iron ochre “paint” at Sunrise for over 13,000 years. From 1900 to 1980, the hematite ore at Sunrise Iron Mine kept the blast furnaces of the Colorado Fuel and Iron steel mill running in Pueblo, Colorado. When the mine shut down due to the early 1980’s steel market, they left behind several million tons of ore on the surface and millions more underground.
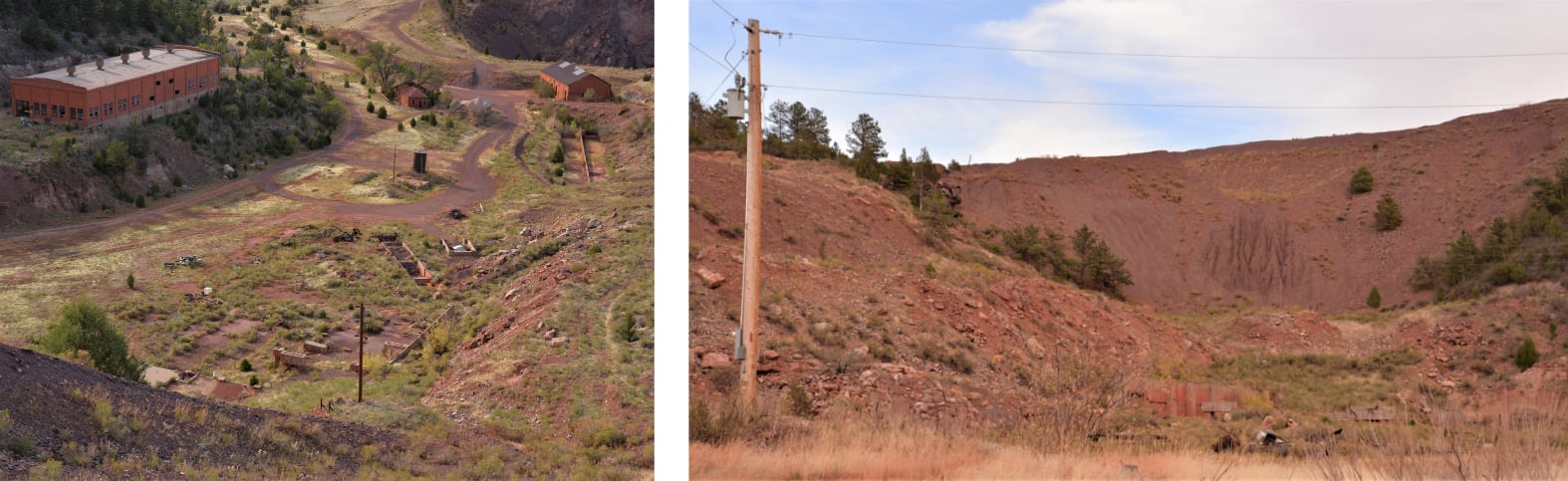
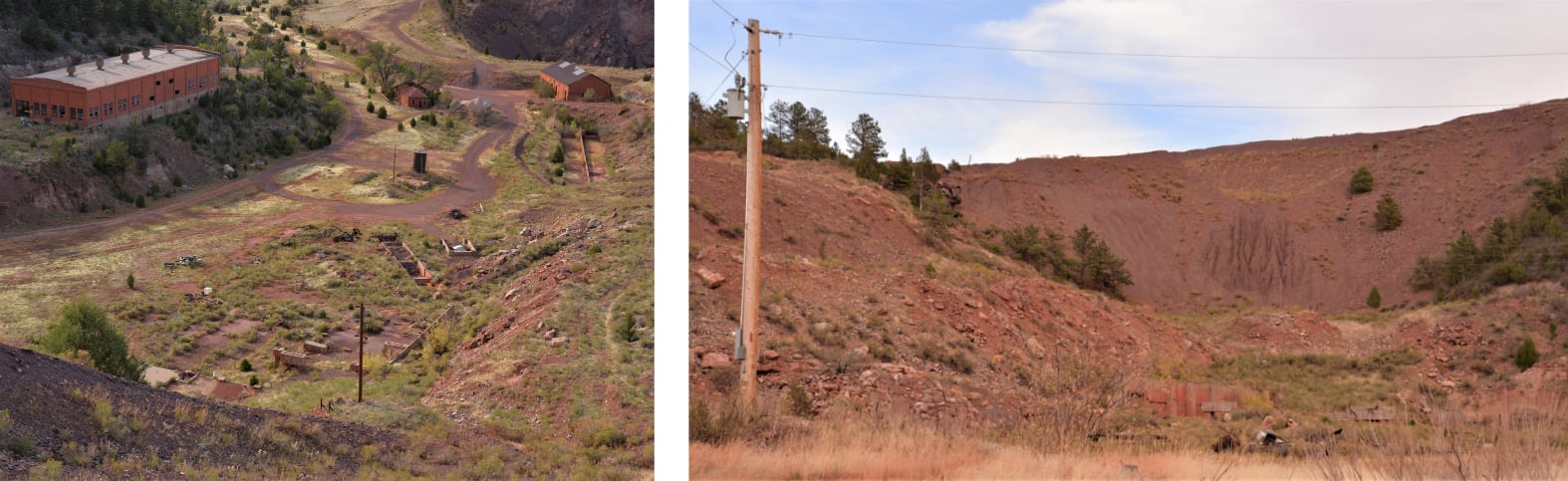
Some might see a legacy of decay; we see a path to a greener future. Let’s take a walk.
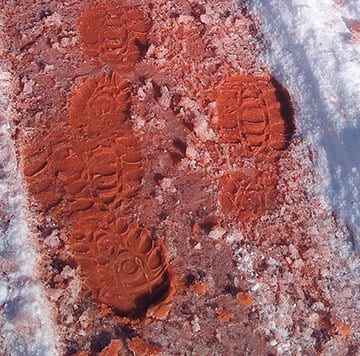
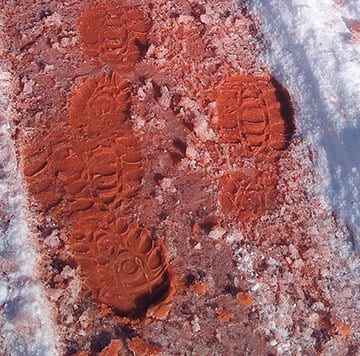
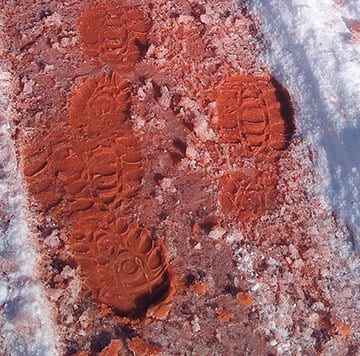
It does not take long to see the potential for iron pigment when walking at Sunrise, it permeates everything. Different colors are possible by mixing iron with other minerals and calcining (baking) at different temperatures. Most pigment now comes from China where mountains of scrap iron are leached with acid. We will simply wash it out of the rock pile. Working with another Wyoming startup, it appears possible to create nano-scale hematite directly in a non-chemical process. This will create better pigment, and potentially, a long-sought-after product for environmental cleanup, groundwater remediation, and EOR.
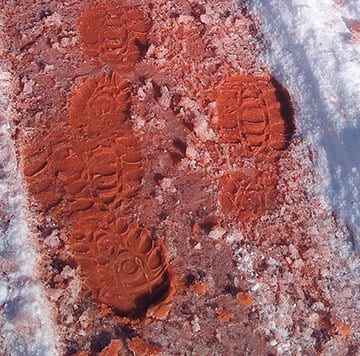
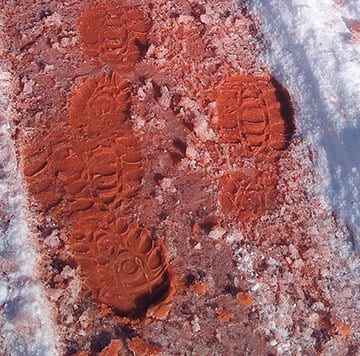
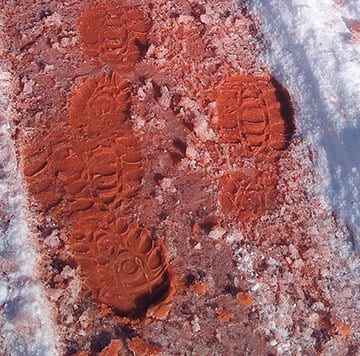